

<< July <<
August <<
September

<< June <<
July <<
August <<
September

<< July <<
August <<
September

<< June <<
July <<
August <<
September

<< June <<
July <<
Aug/Sept

<< Part I
(June/July)
<< Part II
(August)
<< Part I & Part II Bibliography
<< Part III
(September)

<< June <<
July <<
August <<
September

<< June <<
July/August <<
September

<< June << July << August << July/Aug
Bibliography <<
September

<< Part I
(June/July) << Part II
(August) <<Part III
(September) << Bibliography

<< August <<
September
* *   *

Click here to read about the summer's FEATURED ARTISTS!

Visit the site's GUESTS page.

Click here for site NEWS.
* * *

|
|
Essays - July 2012
ALGAL BIOFUELS PART II - GREEN-IN' THE GAS TANK?
" . . . Microalgal biodiesel is technically feasible. It is the only renewable biodiesel that can potentially completely displace liquid fuels derived
from petroleum. Economics of producing microalgal biodiesel need to improve substantially to make it competitive with petrodiesel, but the level of improvement necessary appears to be
attainable."
Yusuf Chisti, "Biodiesel from Microalgae," Biotechnology Advances 25 (2007) (n1)
There is no doubt that lipid-based biofuels from algae can be produced. In the few years since the article cited above appeared, algal biofuel companies have begun to
demonstrate the feasibility of their products through test jet flights and automobile runs. A key advantage of certain algal biofuels is their ability to be used as a "drop-in" fuel substitutes for
petroleum-based products. This means that they can be used exactly as petroleum-based fuels without modification to vehicles or engines as is currently required for ethanol in blends greater than ten percent. But test-run successes of a handful of companies do not make an industry, and
there is still no company producing algal biofuel at a full-scale commercial level. Will algal biofuel or biofuel blends become the home-grown fuel of the future? It may be too early to say, for numerous research and operational challenges
exist. This second part of the Algal Biofuels essay will look in greater depth at the process of creating algal biofuels. The essay will also look at one of the most likely initial uses of the fuel and the
relevance of algal biofuels to California.
Getting from the "Pond" to the Tank

Source: Keynote speech slides, Dr. Richard Sayre, Donald Danforth Plant Science Center, "Microalgae; the Third Generation Biofuel System," 2008. (n2)
Those companies currently producing and testing proprietary types of algal-based fuels are producing them in a variety of ways, and it is too early in the present state of the industry
to say if there is any one "optimal" way of producing algal biofuels. However, there are general stages which are universal to the production process. The chart above provides a more pictoral, though greatly simplified, description of the steps for producing biodiesel from algae. It is
provided as an image to help the reader begin visualizing what the actual process entails. Following below will be a more detailed description of the steps of producing algal biofuel, including challenges faced at each stage of the process.
Step 1: Choosing the Algal Feedstock
The three categories of algae to be considered are 1) macroalgae, or seaweed, 2) cyanobacteria (formerly called blue-green algae) and 3) microalgae (microscopic, photosynthetic organisms). As outlined in the first
part of the essay, most current research and development centers on microalgae as a feedstock for biofuels. Different species of microalgae can vary greatly in terms of percentage of oil content, so selection of algae to be used is a crucial first step, and "understanding, managing and
taking advantage of the biology of algal strains selected for use in production systems is the foundation for processing feedstocks into fuels and [other] products." (n3) (In the original work done through the
Aquatic Species Program, thousands of strains of algae were evaluated and eventually narrowed down to about 300 thought to be suitable for oil production.)
It is possible that different types of algae may be genetically modified to enhance oil production or other traits beneficial to the fuel production process. A survey of information on the
websites of some companies either currently involved in research and development on algal biofuels or producing some type of fuels shows mixed information about genetic modification. Sapphire Energy states on its website that "We use all known bio-agriculture technologies . . . including species selection, trait selection and mutagenesis, and
in the future we will use genetic modification but are not deploying engineered strains at this time." (n4) In 2010 it was reported that Solazyme uses biotechnology to
alter "a single gene [within micro algae] to enhance the already existing pathways inside [the] algal cell . . . [so that it will] overproduce a metabolic by-product: oil." (n5) On the Solazyme website, the company refers to its algae as being "proprietary strains." (n6). Press materials which
appeared on the Synthetic Genomics website in previous years stated that researchers in their program with ExxonMobil will be evaluating "various algae, including both natural and engineered strains, in . . . different growth systems under a wide range of conditions." (n7), though no update to that
information was located on either the ExxonMobil or Synthetic Genomics sites.
In the diagram above, the second stage of biodiesel production is listed as "starve it of nutrients." This is because in early research it was discovered that starving the algal cell of nitrogen (N) or depleting it of silica (Si) (both trace nutrients
required for growth) induced the accumulation of lipids (oils), though only to a certain extent. (n8) These findings became the precursor research to "attempts to manipulate microalgal lipid levels by overexpressing or down-regulating key genes in the lipid or carbohydrate synthetic
pathways." (n9). As photosynthetic organisms, however, the greatest inputs for algal growth are water, (sun)light and carbon, and the interplay of these inputs are an important part in the selection of the means for cultivating algae.
Step 2: Cultivation
In any type of cultivation system for algae, the key objective is high area productivity, or a high photosynthetic efficiency of lipid (oil) production (n10) (in other words, realizing the highest yields in the
shortest possible time (n11)). There are two primary types of cultivation systems for microalgae: heterotrohpic methods, in which algae are grown in fermentation
tanks without light and fed a source of carbon such as sugar for growth (used by Solazyme), and phototropic methods, in which algae are exposed to light in order to grow. Phototrophic cultivation is usually carried out in one of three ways: in large open ponds (though these are used primarily in wastewater treatment), in raceway ponds or in photobioreactors. Most phototrophic
systems used in cultivating microalgae for biofuels are either photobioreactors or raceway ponds. (Macroalgae require different and typically off-shore coastal facilities for growth and will not be discussed here.)

Source: UCSD, San Diego Center for Algae Biotechnology (SD-CAB) Press Kit Photos of 40-acre algae farm just east of the Salton Sea in Imperial Valley near Niland. SD-CAB scientists will demonstrate the feasibility of growing algae for biofuels on a large scale here. On right, mid-sized "raceway" ponds circulate
20,000 - 37,000 gallons of growing algae. Photo credit - Jim Demattia.
The two pictures above are of large and medium-sized raceway ponds. "A raceway pond is made of a closed loop recirculation channel that is typically about .3m deep. Mixing and circulation are produced by a paddlewheel [and] flow is
guided around bends by baffles placed in the flow channel. Raceway channels are built in concrete, or compacted earth, and may be lined with white plastic. During daylight, the culture is fed continuously in front of the paddlewheel where the flow begins . . . [and] harvested behind the paddlewheel on completion
of the circular loop." (n12) (To view an aerial photo of a large algal cultivation farm, visit the site of the Hawaii-based company Cyanotech - www.cyanotech.com and go to company/facility. The company produces algae for neutraceuticals [not fuels], but thier facility photo
provides a good depiction of the size/scope of a large algal cultivation facility using open ponds.) Photobioreactors are essentially closed systems which are exposed to light but have a water flow maintained by a source such as a mechanical pump and have carbon dioxide and other nutrients added to the system. Photobioreactors are generally classified as
tubular, vertical column or flat plate (n13). Both types of systems have their advantages and drawbacks, and chart comparing some features of cultivation approaches is included
below.

Source: US DOE, Office of Energy Efficiency and Renewable Energy, National Algal Biofuels Technology Roadmap, May 2010. (n14)
In addition to the benefits/drawbacks of certain cultivation systems, algae also have inherent physiological limitations which include limited biosynthetic growth rates, an narrow optimum temperature range for growth, a limited rate at which
atmospheric CO2 can diffuse into a culture system, nutrient limitations, and self-shading during growth (cells nearer the light source absorb more light preventing it from reaching more distal cells, which is why cultures must be continually mixed). (n15) While the "theoretical maximum growth rate for
algae is approximately 100 g/m2/day, . . . [due to certain limitations such as the ones included above] high values of productivity observed over extended periods in both open and closed systems [have] tend[ed] to fall within the range of 20-30 g/m2/day based on [the] illuminated culture surface
area." (n16) Observations to date indicate that "of the two major types of large-scale algae cultures systems, open ponds have a low productivity compared to photobioreactors, [and though] photobioreactors require a high initial capital investment, [they] appear to be able to
produce biomass at a lower price. (n17) Overall, "designing an optimum cultivation system involves leveraging the biology of the algal strain used and integrating it with the best-suited downstream processing options [to be discussed below]. Choices made for the cultivation system are key to the affordability, scalability and
sustainability of [the] algal to biofuel system." (n18)
Step 3 and 4: Harvesting, Dewatering and Oil Extraction
Once the algal growth cycle is complete, algae must be harvested and usually dewatered (excess water removed) to a certain extent before the oil can be extracted and the algae sent for final processing. This process of harvesting and dewatering would sit between steps number two and three through five on the
chart above. While a full technical description of the process and technologies involved would be beyond the scope of this essay, a few key concepts and terms relevant to understanding these steps in the process of biofuel production will be presented.
Harvesting, dewatering and oil extraction are energy-intensive processes, and one challenge on the road to creating algal biofuels is to optimize the handling/drying/conversion process in a manner that consumes less energy than what is contained in the
algal products. (n19) After an algal culture reaches maturity, the biomass "carries a high water content and, in most cases, is not suited for conversion to biofuel products until it has undergone some degree of dewatering and drying." (n20) In order to harvest microalgae, the diluted algal suspension must be
concentrated into a thicker "broth" or "paste." (n21) For example, the algal concentration of microalgae grown in open ponds is typically about 0.02 - 0.06 percent total solid matter. (n22) The aim of harvesting is to obtain a "slurry with at least a 2 - 7 percent algal suspension on [a] dry matter
basis. (n23)
Flocculation/sedimentation and dissolved air flotation are biomass recovery/harvesting techniques applied primarily to open pond cultivation systems, while filtration and centrifugation are methods applied primarily to algae grown in photobioreactors. (n24) The terms are
defined below:
Flocculation: The process, often implemented with the help of . . . flocculants (chemicals of natural or synthetic origin) that cause the coagulation of algal cells into small
clumps . . . allowing for sedimentation and easy extraction from the culture. (n25)
Dissolved Air Flotation: Usually used in conjunction with flocculation, it was a process originally established for sewage treatement but applied to algal harvesting. With dissolved air flotation, "Air is bubbled through
the [algal] suspension causing the algal clusters to float to the surface where they can be removed" by a skimming device. (n26)
Centrifugation: "A centrifuge, generally driven by a motor, puts the algal culture in motion (applying force) to evenly distribute the water and biomass by greater and lesser density. Centrifugation is typically
a high-energy process considered impractical for large-scale algal harvesting; however, large industrial centrifuges are commonly used in water and wastewater treatment to dry sludge. (n27)
(Micro)Filtration: "Microfiltration, or microscreening, is a basic approach to biomass recovery whereby algal cells are filtered through microscreens to be sparated from the growth culture . . . Vibrating microscreens are rotating, backwashed fine-mesh screens
with the ability to harvest continuously and by cell size (i.e. maturity). This helps to maximize yields because immature algae are passed through, leaving mature, oil-rich algae to be harvested . . . Microfiltration does not necessarily employ chemicals and does not require treatment of filtered water before it is recycled to the cultivation system along with
the immature, unharvested algal cells. (n28)
Should any additional drying be necessary prior to subsequent processing, it can be accomplished by any of a number of techniques including solar drying, drum drying, freeze drying, etc. Since "the harvesting, dewatering and extraction steps are closely linked, . . . the extraction process conditions will dictate to what extent
water must first be removed in the dewatering process." (n29) Referring again to the chart above, it indicates that cell rupture (breaking the cell open) is the means for extracting algal oils, when it is only one of several possible options for extracting and separating algal oils from other algal cell components. "After the dewatering process,
lipids can be recovered from the algal biomass by means of physical (mechanical disruption) processes, chemical (solvent extraction) processes, or both. Chemical extraction, typically using a chloroform/methanol/water or hexane solvent system . . . is more effective and preferred on a laboratory scale. However, because this method is difficult to scale [up to a
commercial level], researchers are focusing on reducing the use of toxic and polluting solvents and [testing] environmentally-friendly extraction methods. New lipid-extraction technologies involve innovations in acoustics, sonication, mesopourous nanomaterials and [other types of] solvents." (n30)

"Green Crude." Source: Sapphire Energy, Inc. Media materials
Steps 5 and 6: Oil Conversion and End Products
In the final stage of the algae to biofuels production, lipids, carbohydrates and/or other portions of the algal biomass are converted by a number of
different processes to create a variety of fuels and other end products or by-products. Some of those processes and end-products are outlined in the last two columns of the chart below. Thought the technical details of
each process or pathway to fuel conversion will not be discussed in greater detail here, those interested can find a more in-depth description in the Chapter 6, Algal Biofuel Conversion Technologies, section of the National
Algal Biofuels Technology Roadmap Report. In general, the pathways for converting algal biomass to fuels fall into one of three categories:
1) Those that focus on the direct algal production of recoverable fuel molecules (eg. ethanol, hydrogen, methane and alkanes) from algae without
the need for extraction
2) Those that process whole algal biomass to yield fuel molecules
3) Those that process algal extracts (eg. lipids, carbohydrates) to yield fuel
molecules (n31)
Instead of discussing individual processes here, the concept of a biorefinery will be introduced, for three of the companies included in the company list further down the page, Algenol Biofuels,
Solazyme and Sapphire Energy, have received funding from the U.S. Department of Energy for either demonstration-scale or pilot-scale integrated biorefinery
projects.
In a petroleum refinery, "all of the procsses that take place . . . can be divided into two categories, separation and modification of the components in crude oil to yield an assortment of
end products. The fuel products are a mixture of components that vary based on the input stream and process steps, and . . . are . . . defined by their performance specifications." (n32) A biorefinery is "a facility that integrates biomass conversion
processes and equipment to produce fuel, power and value-added chemicals from biomass . . . By producing multiple products, a biorefinery takes advantage of the various components of biomass raw materials and their intermediates, therefore maximizing the value derived
from the biomass feedstock." (n33) The goal for biorefineries is to "produce both high-volume liquid fuels and high-value chemicals or products in order to address national energy needs while enhancing
operational economics." (n34)
The U.S. Department of Energy, Energy Efficiency and Renewable Energy, defines pilot-scale projects as those for screening and validating promising technologies and
typically processing at least one dry metric ton of feedstocks per day. Demonstration-scale projects are those which have been validated at a pilot scale and are ramped up to process a minimum of 50 dry metric tons of feedstock
per day (representing 1/50 to 1/10 commercial scale). (n35) The three algal fuel biorefineries which have received funding are:
Algenol Biofuels - Integrated PILOT SCALE biorefinery for producing ethanol from hybrid algae. A biorefinery will
be constructed to convert carbon dioxide into ethanol. Algenol is targeting the development of hybrid algae that produce 6,000 gallons of ethanol per acre per year. The biorefinery will consume two dry tons of
carbon dioxide per day and produce more than 100,000 gallons of ethanol per year.
Solazyme - Integrated PILOT SCALE biorefinery for heterotrophic algal oil biomanufacturing. The biorefinery will validate the projected commercial-scale
economics of producing multiple advances biofuels and collect the data necessary to complete design of the first commercial-scale facility. The project also will demonstrate the production of algal oil derived entirely
from lignocellulosic and other feedstocks.
Sapphire Energy - Integrated DEMONSTRATION-SCALE biorefinery. The facility will reuse carbon dioxide to produce green crude oil from algae. The oil will be
refined to produce jet fuel and diesel.
A full listing of all the commercial-, demonstration- and pilot-scale biorefinery projects (not just algal-related) which have received funding can be found at
www1.eere.energy.gov/biomass/pdfs/ibr_portfolio_overview.pdf. They are also described more fully in the Biorefinery section of the 2011 Biomass Energy Data
Book which can be viewed online or downloaded from http://cta.ornl.gov/bedb.
One final note on biorefineries, and that is in regard to Sapphire Energy. To date, Sapphire Energy appears to be the only algal biofuel company producing
significant amounts of not only biodiesel but what it refers to as "green crude" (oil). If selection of executive expertise is any indication of the importance of certain aspects of the fuel production process to the company, then Sapphire Energy appears
to place great importance on the refining aspect of biofuel production. They have selected as President/CEO a woman named Cynthia Warner, one of the few senior women in the oil and gas industry, and one with more than 20 years of experience in the
industry, particularly in petroleum refining operations. Her full resume can be viewed on the company's website.
The full process of creating fuel from algae can be summarized via the chart below:
 |
• Type of algae:
- Microalgae
- Cyanobacteria
- Macroalgae
• Genetic Modification?
• CO2, Water
• Nutrients
• Sunlight, etc.
|
• Open Pond
• Raceway Pond
• Photo-
bioreactor
• Fermentation
Tank
• Marine
System (For
Macroalgae)
|
• Flocculation
• Dissolved Air
Flotation
• Filtration/
Microscreening
• Centrifugation
• Drying
• Other
|
• Physical (Cell
Rupture)
• Chemical
• Solvent
• Microwave
• Enzymatic
• Other
|
• Transesteri-
fication
• Fermentation
• Pyrolysis
• Gasification
• Enzymatic
Conversion
• Liquefaction
•Other refining
Methods
|
• "Green" Fuel:
- Jet Fuel
- Gasoline
- Diesel
• Biodiesel
• Ethanol
• Animal Feed
• Food
Additives
• Fertilizer |
Source: Adapted from Don O'Connor/Consultants Inc., IEA Bioenergy Task 39, Algae as a Feedstock for Biofuels, Sept. 2011, and US DOE, Office of Energy Efficiency
and Renewable Energy, National Algal Biofuels Technology Roadmap, May 2010. (n36)
Green-In' Which Tank?
It is still early to say what quantities of algal biofuels will be able to be produced in the near- to mid-future, but it is more likely that consumers first will encounter the fuels in the tank of a plane on an upcoming flight than in
their own personal gas tanks. Jet fuels may be the largest early market for algal (and certain other) biofuels. One author describes the situation facing the aviation industry as follows:
"Whereas land-based transport could in theory be completely electrified [or] powered by batteries charged from renewable sources, there is no alternative to energy-dense liquid fuels for
jet engines . . . If airlines are to have any chance of staying aloft in a post-peak [oil], carbon-rationed world, they must quickly find an alternative fuel with low emissions that also matches the stiff technical standards of jet kerosene. Because planes have to lift their fuel into the sky and
carry it for the entire journey, this fuel has to be energy dense. Because they fly at high altitude, it needs to remain fluid at -50 degrees C. Because they fly long distances, chemically identical supplies must be available all over the world. And because airlines have long lives, the new fuel
must be compatible with the existing fleet. What's needed, in other words, is an exact replica of old-fashioned jet kerosene - a so-called 'drop-in' replacement - that also emits substantially less CO2 per unit of energy." (n37)
This need is recognized in both commercial and military jet fuel markets. In the U.S. for example, more than 50 percent of total Department of Defense energy use is jet fuel, for which many lower-density biofuels like ethanol are not suitable
replacements. (n38). In the commercial market, Boeing forecasts the number of airplanes in service to increase from about 20,000 in 2011 to nearly 40,000 in 2031, (n39) with a corresponding need for fuels which are both sustainable and able to reduce
life-cycle emissions compared to conventional fuels. (n40)
The issue is being addressed on many levels. Groups like CAAFI in the U.S. (Commercial Aviation Alternative Fuels Initiative, www.caafi.org) are working to enhance energy
security and environmental sustainability through alternative jet fuels. The International Air Transport Association (IATA, www.iata.org or
www.iataonline.com) in December of last year published its 2011 Report on Alternative Fuels detailing global efforts and measures being taken with regard to alternative
jet fuels. (n41) Also, since the ASTM (international standards organization setting jet fuel standards) approved the commercial use of jet fuel blends, "conventional jet fuel blends with up to 50 percent biofuel derived
from sources such as jatropha, camelina, algae and other oils have been used on more than 1,500 commercial jet flights." (n42).
Early indications are that private companies are beginning to stake out positions in the emerging jet biofuels market as well. One such company is BioJet International
(www.biojetcorp.com). BioJet defines itself as "the leading international supply chain integrator for renewable (bio) jet fuel and related co-products." (n43) Formed in 2008, "BioJet was the
first company to operate across the entire supply chain by owning and controlling large quantities of bio-feedstock, developing refining/conversion capacity, solving aviation fuel supply logistics and handling sales to end users." (n44) Company
materials state that BioJet is "fundamentally agnostic with regard to feedstocks and is committed to utilizing any and all sustainable and economically viable sources," (n45) and its interests include jatropha, camelina, algae and waste
biomass. In 2011 alone, BioJet:
Received a $1.2 billion financing facility from Equity Partners Fund
Acquired Abundant Biofuels Corp., making it the world's largest jatropha feedstock developer
Formed an exclusive relationship with the Council of Energy Resource Tribes (CERT) to develop renewable jet and diesel
feedstock and refining facilities on Native American lands
Gained exclusive worldwide rights to disruptive Camelina crop yield technology which is expected
to double Camelina crop yields
Offered one billion gallons of renewable jet fuel to the industry at a $3 price cap on future deliveries
Formed the BioJet Asia Pac subsidiary to develop aviation biofuels in China and the Asia Pacific domain. (n46)
In a news release the company's Chairman, Mitch Hawkins, said of the deal with CERT that he envisions the business relationship "to include at least $1 billion worth of joint
projects over a ten-year period locating feedstock generation and refining operations to provide biofuels for commercial airlines and ground transportation at key locations throughout the western United States." (n47)
Niche Industry or the Next Big Thing in Biofuels?
"By mid 2010, an estimated 200 companies were directly participating in algal biofuels production, rising from virtually no companies at the start of the
decade, . . . [and in that same period] the industry grew from miniscule in value . . . to reach an estimated market value of $271 million." (n48) Some of the industry's most well-known companies and their
website links are included below.
Algenol Biofuels
Aquaflow
Aurora Algae, Inc.
Bioalgene
Bionavitas, Inc.
Bodega Algae, LLC
LiveFuels, Inc.
PetroAlgae Inc.
Phyco Biosciences
Sapphire Energy, Inc.
Seambiotic Ltd.
Solazyme, Inc.
Solix Biofuels, Inc.
Synthetic Genomics Inc.
|
Bonita Springs, FL
Nelson, New Zealand
Hayward, CA
Seattle, WA
Redmond, WA
Boston, MA
San Carlos, CA
Melbourne, FL
Chandler, AZ
San Diego, CA
Tel Aviv, Israel
S. San Francisco, CA
Fort Collins, CO
La Jolla, CA
|
www.algenolbiofuels.com
www.aquaflowgroup.com
www.aurorainc.com
www.bioalgene.com
www.bionavitas.com
www.bodegaalgae.com
www.livefuels.com
www.petroalgae.com
www.phyco.net
www.sapphireenergy.com
www.seambiotic.com
www.solazyme.com
www.solixbiofuels.com
www.syntheticgenomics.com
|
Source: Yusuf Chisti and Jinque Yan, "Energy From Algae: Current Status and Future Trends. Algal Biofuels - A Status Report." Applied Energy 88 (2011) (n49)
Given that to date no full-scale commercial production facilities exist (Sapphire Energy has said it expects to reach full-scale commercial operations in 2018
(n50)), future algal biofuel production projections vary greatly. Emerging Markets Online has projected production of between 100 million and
one billion gallons of algal biofuels by 2015 (n51), while Pike Research has projected a more modest 61 million gallons of algal biofuels to be produced by 2020. (n52) Current estimates
place the cost of today's algal biofuels to be the equivalent of about $200 - $1,200 US/bbl of crude oil, with some future cost estimates as low as a $60/bbl equivalent of crude oil. (n53) At the time this essay was written,
crude oil prices stood at about $92/bbl (and jet fuel at about $117/bbl), and some claim oil from algae is likely to be financially viable "in a scenario with crude petroleum selling for more than $100 per barrel." (n54) What is always impossible to factor into
the equation is the impact of possible scientific breakthroughs or unexpected developments in the industry (say, for example, if Oracle's Larry Ellison decided to give new life to an old plantation by turning his recent Hawaiian island purchase into a large
algal biofuel test production facility).
What does this mean for California? Several of the companies listed above may be headquartered in the state, but their production and/or refining facilities may be located elsewhere. The industry is likely to have a
significant presence in the San Diego area, as one of the country's largest algal research consortiums, the San Diego Center for Algae Biotechnology (SD-CAB, www.algae.ucsd.edu), is located in the city based out of U.C. San Diego. SD-CAB was
"established in 2008 as a consortium of researchers from the University of California, San Diego (UCSD), Scripps Institution of Oceanography (SIO) and San Diego State University (SDSU), in partnership with private industry . . . The mission of SD-CAB is to support development of innovative,
sustainable, and commercially viable algae-based biotechnology solutions for energy, green chemistry, bio-products, water conservation and CO2 abatement challenges," and the consortium hold an annual Biofuels Symposium. (n55). In June of this year, the 2nd International Conference
on Algal Biomass, Biofuels and Bioproducts also was held in San Diego, and you can find information on the conference themes and particpants at www.algalbbb.com.
A Natural Resources Defense Council (NRDC) report said this of the overall algal biofuels industry:
"Algae-derived gasoline, diesel and jet fuel sound like the imaginings of science fiction, but a growing number of entrepreneurs, investors, academics and policy makers are trying to make
them reality. The economic, national security and environmental costs of our dependence on oil become clearer every day, and algae may be able to provide large quantities of locally produced biofuels with minimal environmental impacts. The algal biofuels industry is comprised of many pathways to produce fuels from
algae and is developing rapidly, with most companies operating in 'stealth' mode. This makes measuring progress toward the promise of algae extremely difficult. Given the thousands of different algal strains, multitude of cultivation and harvest methods, wide range of algae products, and
host of technologies used to convert these products into different transportation fuels, algae-based biofuels make up a broad and difficult-to-categorize family of technologies and
production pathways. Furthermore, technologies are evolving rapidly." (n56)
As said before, there is no question that is it feasible to make fuel from algae and that certain algal biofuels can be used effectively as "drop-in" replacements for
petroleum-based products. Whether or not the fuels can be produced cost effectively and reliably in large quantities over the long term and still be competitive with both conventional and other alternative fuels remains to be seen. The road from "pond scum" to "green crude" or
algal biodiesel industry may still be a risky long one, but it appears to be a path both companies and investors are willing to take.

FOOTNOTES
- The following are the footnotes indicated in the text in parentheses
with the letter "n" and a number. If you click the asterisk at the end of
the footnote, it will take you back to the paragraph where you left
off.
n1 - Chisti, Yusuf, "Biodiesel from Microalgae," Biotechnology Advances 25 (2007), p. 304. (*)
n2 - Sayre, Dr. Richard, "Microalgae: The Third Generation Biofuel System," Keynote Speech Slides, Donald Danforth Plant Science Center: 2008. Available online at
http://www.orau.gov/algae2008pro/presentations/keynote/keynote_3rd%20Generation%20Biofuels.pdf. (*)
Photo: Algae Growing in a Flask in a Lab at SD-CAB, photo courtesy of SD-CAB press kit photos
n3 - U.S. Department of Energy, Office of Energy Efficiency and Renewable Energy, Office of the Biomass Program, National Algal Biofuels Technology Roadmap, Washington, D.C.:
U.S. Department of Energy: May 2010, p. iv (*)
n4 - Sapphire Energy FAQ; viewed online July 2012 at www.sapphireenergy.com/learn. (*)
n5 - Templer, Laura, "Synthetic Biology: Injecting New Life Into the Chemical Industry," Chemical Week, Vol. 172, No. 30, December 13, 2010,
p. 24 (*)
n6 - Viewed online July 2012 at www.solazyme.com (*)
n7 - Synthetic Genomics, "ExxonMobil and SGI Advance Algae Biofuels Program with New Greenhouse," press release dated July 14, 2010, viewed online
August 2011 at www.syntheticgenomics.com/media/press/071410.html (*)
n8 - Sheehan, John, Dunahay, Terri, Benemann, John and Roessler, Paul. A Look Back at the U.S. Department of Energy's Aquatic Species Program -
Biodiesel from Algae, NREL/TP-580-24190, Golden, CO: NREL, July 1998, Part II: Technical Review, p. 3 (*)
n9 - Ibid. (*)
n10 - Rodolfi, Liliana, Chini Zittelli, Graziella, Bassi, Niccolo, Padovani, Giulia, Biondi, Natascia, Bonini, Gimena, and Tredici, Mano R., "Microalgae for Oil: Strain
Selection, Induction of Lipid Synthesis and Outdoor Mass Cultivation in a Low-Cost Photobioreactor," Biotechnology and Bioengineering, Vol. 102, January 1, 2009, p. 102. (*)
n11 - Grobbelaar, Johan U., "Factors Governing Algal Growth in Photobiorectors: The "Open" versus "Closed" Debate," Journal of Applied Phycology 21 (2009),
p. 490 (*)
n12 - Chisti, "Biodiesel from Microalgae," p. 297 (*)
n13 - Ugwu, C.U., Aoyagi, H., and Uchiyama, H., "Photobioreactors for Mass Cultivation of Algae," Bioresource Technology 99 (2008),
p. 4022 (*)
n14 - U.S. Department of Energy, National Algal Biofuels Technology Roadmap, p. 29 (*)
n15 - Darzins, Al and Pienkos, Philip and Edye, Les, Current Status and Potential for Algal Biofuels, A Report to the IEA Bioenergy Task 39, Report T39-T2, 6 August
2010, pp. 19 - 20. Report is available online at www.task39.org (*)
n16 - Ibid. p. 19(*)
n17 - Chisti, Yusuf, and Yan, Jinque, "Energy from Algae: Current Status and Future Trends. Algal Biofuels - A Status Report," Applied Energy 88 (2011)
p. 3277(*)
n18 - U.S. Department of Energy, National Algal Biofuels Technology Roadmap, p. iv (*)
n19 - Ibid., p. v (*)
n20 - Ryan, Catie/National Resources Defense Council (NDRC), Cultivating Clean Energy: The Promise of Algal Biofuels, New York/Washington D.C.: National Resources Defense Council, October
2009, p. 47. Available online at www.ascension-publishing.com/BIZ/cultivating.pdf. (*)
n21 - Singh, Anoop, Poonam, Singh Nigam, and Murphy, Jerry D., "Mechanism and Challenges in Commercialization of Algal Biofuels," Bioresource Technology 102
(2011), p. 30 (*)
n22 - Ibid. (*)
n23 - Ibid. (*)
n24 - Ibid. (*)
n25 - Ryan, Catie/National Resources Defense Council (NDRC), Cultivating Clean Energy: The Promise of Algal Biofuels, p. 44 (*)
n26 - U.S. Department of Energy, National Algal Biofuels Technology Roadmap, p. 37 - 38 (*)
n27 - Ryan, Catie/National Resources Defense Council (NDRC), Cultivating Clean Energy: The Promise of Algal Biofuels, p. 46 (*)
n28 - Ibid. (*)
n29 - Knoshang, Eric P and Darzins, Al, "Algal Biofuels: The Process," Chemical Engineering Progress, 107:3, March 2011, p. 41 (*)
n30 - Cheng, Kuan-Chen and Ogden, Kimberly L., "Algal Biofuels: The Research," Chemical Engineering Progress, 107:3, March 2011, p. 45 (*)
n31 - U.S. Department of Energy, National Algal Biofuels Technology Roadmap, p. 48 (*)
n32 - Ibid., p. 56 (*)
n33 - Subhadra, Bobban G., "Sustainability of Algal Biofuel Production Using Integrated Renewable Energy Park (IREP) and Algal Biorefinery Approach,"
Energy Policy 28, (2010), p. 5893 (*)
n34 - Boundy, Bob, Diegel, Susan W., Wright, Lynn and Davis, Stacy C., Biomass Energy Data Book, Edition 4, Oak Ridge, Tennessee: Oak Ridge National Laboratory, September 2011, Biorefineries Overview. Data book can
be downloaded from http://cta.ornl.gov/bedb. (*)
n35 - U.S. Department of Energy, Office of Energy Efficiency and Renewable Energy, Biomass Program, "Integrated Biorefineries: Biolfuels, Biopower and Bioproducts," DOE/EE-0767, July 2012, p. 3. Viewed online/downloaded July 2012 at
www1.energy.gov/biomass/pdfs/ibr_portfolio_overview.pdf. (*)
n36 - O'Connor, Don/Consultants, Inc., IEA Bioenergy Task 39, Algae as a Feedstock for Biofuels: An Assessment of the Current Status and Potential for the
Algal Biofuels Program, September 2011, p. 5 (available online at www.task39.org, and portions of U.S. Department of Energy, National Algal Biofuels Technology Roadmap (*)
n37 - Strahan, David, "A Tank of the Green Stuff," New Scientist, Vol. 199, No. 2669, 16 August 2008, p. 35 (*)
n38 - U.S. Defense Logistics Agency, Green Initiative for Fuels Transition Pacific, presentation chart statistic, available online at
www.usda.gov/documents/morning_speaker_PACOM.pdf (*)
n39 - Boeing, Current Market Outlook: 2012 - 2031. Seattle, WA: Boeing Commercial Airplanes, 2012, p. 4. Available online at
www.boeing.com/commercial/cmo/pdf/Boeing_Current_Market_Outlook_2012.pdf. (*)
n40 - Boeing, Current Market Outlook: 2012 - 2031, p. 10 (*)
n41 - International Air Transport Association (IATA), IATA 2011 Report on Alternative Fuels. IATA: Montreal, Quebec and Geneva, Switzerland 2011. Available online at
www.iata.org/whatwedo/environment/Documents/IATA%202011%20Report%20on%20Alternative%20Fuels.pdf, or by searching "Alternative Fuels Report" at www.iata.org. (*)
n42 - Boeing, Current Market Outlook: 2012 - 2031, p. 10 (*)
n43 - Viewed online July 2012 at www.biojetcorp.com (*)
n44 - International Air Transport Association (IATA), IATA 2011 Report on Alternative Fuels, p. 51 (*)
n45 - www.biojetcorp.com/feedstocks.php, viewed online July 2012 (*)
n46 - International Air Transport Association (IATA), IATA 2011 Report on Alternative Fuels, p. 51 (*)
n47 - BioJet International, Press Release - "Council of Energy Resource Tribes and BioJet form Strategic Alliance," BioJet website, viewed online July 2012 at
www.biojetcorp.com/reports/CERT-BioJet%20Press%20Release%201-10-12.pdf (*)
n48 - O'Connor, Don/Consultants, Inc., Algae as a Feedstock for Biofuels, p. 5 (*)
n49 - Chisti, Yusuf, and Yan, Jinque, "Energy from Algae: Current Status and Future Trends. Algal Biofuels - A Status Report," p. 3278 (*)
n50 - Sapphire Energy FAQ; viewed online July 2012 at www.sapphireenergy.com/learn.(*)
n51 - O'Connor, Don/Consultants, Inc., Algae as a Feedstock for Biofuels, p. 5. General information also at www.emerging-markets.com/algae. (*)
n52 - Pike Research, news story October 27, 2010, viewed online July 2012 at
www.pikeresearch.com/newsroom/algae-based-biofuels-production-to-reach-61-million-gallons-per-year-by-2020 (*)
n53 - O'Connor, Don/Consultants, Inc., Algae as a Feedstock for Biofuels, p. 5. (*)
n54 - Chisti, Yusuf, and Yan, Jinque, "Energy from Algae: Current Status and Future Trends. Algal Biofuels - A Status Report," p. 3277 (*)
n55 - San Diego Center for Algae Biotechnology (SC-CAB) brochure; viewed online July 2012 at www.algae.ucsd.edu/_files/SDCAB_Brochure.pdf (*)
n56 - Ryan, Catie/National Resources Defense Council (NDRC), Cultivating Clean Energy: The Promise of Algal Biofuels, p. iv, Introductory Letter (*)

LINKS LIST - The following is a list of links external to the website found in the essay.
1. Cyanotech Company Website - www.cyanotech.com
2. U.S. Department of Energy, EERE/Biomass Biorefinery Project Information -
www1.eere.energy.gov/biomass/pdfs/ibr_portfolio_overview.pdf
3. Oak Ridge National Laboratories, 2011 Biomass Energy Data Book - http://cta.ornl.gov/bedb
4. Commercial Aviation Alternative Fuels Initiative (CAAFI) - www.caafi.org
5. International Air Transport Association (IATA) - www.iata.org
6. BioJet International - www.biojetcorp.com
7. Algal Biofuel Industry Company Website Links (14 companies, see chart in essay)
8. San Diego Center for Algae Biotechnology (SD-CAB) - www.algae.ucsd.edu
9. Algal Biomass, Biofuels and Bioproducts Conference - www.algalbbb.com

BIBLIOGRAPHY - The combined Bibliography for the June and July Algal Biofuels essays is included below.
BioJet International, Press Release - "Council of Energy Resource Tribes and BioJet form Strategic Alliance," BioJet website, viewed online July 2012 at
www.biojetcorp.com/reports/CERT-BioJet%20Press%20Release%201-10-12.pdf
Boeing, Current Market Outlook: 2012 - 2031. Seattle, WA: Boeing Commercial Airplanes, 2012, p. 4. Available online at
www.boeing.com/commercial/cmo/pdf/Boeing_Current_Market_Outlook_2012.pdf.
Boundy, Bob, Diegel, Susan W., Wright, Lynn and Davis, Stacy C., Biomass Energy Data Book, Edition 4, Oak Ridge, Tennessee: Oak Ridge National Laboratory, September 2011, Biorefineries Overview. Data book can
be downloaded from http://cta.ornl.gov/bedb.
Cheng, Kuan-Chen and Ogden, Kimberly L., "Algal Biofuels: The Research," Chemical Engineering Progress, 107:3, March 2011,
pp. 42 - 47
Chisti, Yusuf, "Biodiesel from Microalgae." Biotechnology Advances 25 (2007), pp. 294 - 306.
Chisti, Yusuf, and Yan, Jinque, "Energy from Algae: Current Status and Future Trends. Algal Biofuels - A Status Report," Applied Energy 88 (2011)
pp. 3277 - 3279.
Commodity Research Bureau, CRB Commodity Yearbook 2009, Chicago, IL: Commodity Research Bureau, 2009
Darzins, Al and Pienkos, Philip and Edye, Les, Current Status and Potential for Algal Biofuels, A Report to the IEA Bioenergy Task 39, Report T39-T2, 6 August
2010. Report is available online at www.task39.org.
Gouveia, Luisa and Oliveira, Ana Cristina, "Microalgae as a Raw Material for Biofuels Production," Journal of Industrial Microbiology and Biotechnology (2009) 36: 269 - 274.
Grobbelaar, Johan U., "Factors Governing Algal Growth in Photobiorectors: The "Open" versus "Closed" Debate," Journal of Applied Phycology 21 (2009),
pp. 489 - 492.
HR BioPetroleum, news releases, "HR BioPetroleum to Acquire Shell's Shareholding in Cellana Algae Joint Venture," January 27, 2011, viewed online
June 2012 at http://cellana.com/news/hr-biopetroleum-to-acquire-shells-shareholding-in-cellana-algae-joint-venture
International Air Transport Association (IATA), IATA 2011 Report on Alternative Fuels. IATA: Montreal, Quebec and Geneva, Switzerland 2011. Available online at
www.iata.org/whatwedo/environment/Documents/IATA%202011%20Report%20on%20Alternative%20Fuels.pdf, or by searching "Alternative Fuels Report" at www.iata.org.
International Energy Agency (IEA), "IEA Energy Technology Essentials: Biofuel Production," Paris: OECD/IEA, January 2007, p. 3. Available online
at www.iea.org/Textbase/techno/essentials.htm
Jorquera, Orlando, Kiperstok, Asher, Sales, Emerson A., Embirucu, Marcelo, and Ghirardi, Maria L., "Comparative Energy Life-Cycle Analyses of Microalgal Biomass Production in Open Ponds
and Photobiorectors," Bioresource Technology 101 (2010), pp. 1406 - 1413.
Khosla, Vinod, White Paper: What Matters in Biofuels and Where Are We?", January 27, 2011. Viewed online June 2012 at
www.khoslaventures.com/wp-content/uploads/2012/02/What_Matters_in_Biofuels_2011.pdf.
Knoshang, Eric P and Darzins, Al, "Algal Biofuels: The Process," Chemical Engineering Progress, 107:3, March 2011, pp. 37 - 47.
Malcata, R. Xavier, "Microalgae and Biofuels: A Promising Partnership?" Trends in Biotechnology Vol. 29, No. 11, November
2011
O'Connor, Don/Consultants, Inc., IEA Bioenergy Task 39, Algae as a Feedstock for Biofuels: An Assessment of the Current Status and Potential for the
Algal Biofuels Program, September 2011. (Available online at www.task39.org.)
Renewable Fuels Association, "Industry Statistics," viewed September 2008 at www.ethanolrfa.org/industry/statistics.
Rodolfi, Liliana, Chini Zittelli, Graziella, Bassi, Niccolo, Padovani, Giulia, Biondi, Natascia, Bonini, Gimena, and Tredici, Mano R., "Microalgae for Oil: Strain
Selection, Induction of Lipid Synthesis and Outdoor Mass Cultivation in a Low-Cost Photobioreactor." Biotechnology and Bioengineering, Vol. 102, January 1, 2009, pp. 100 - 112.
Rotman David, "The Price of Biofuels," Technology Review, Vol. 111, No. 1, January/February 2008, pp. 42 - 46.
Royal Dutch Shell, Shell Global media releases, "Shell and HR Biopetroleum build facility to grow algae for biofuel," November 12, 2007; viewed online
June 2012 at http://www.shell.com/home/content/media/news_and_media_releases/archive/2007/biofuels_cellana_11122007.html.
Ryan, Catie/National Resources Defense Council (NDRC), Cultivating Clean Energy: The Promise of Algal Biofuels, New York/Washington D.C.: National Resources Defense Council, October
2009. Available online at www.ascension-publishing.com/BIZ/cultivating.pdf.
Sapphire Energy, Sapphire Energy FAQ. Viewed online July 2012 at www.sapphireenergy.com/learn.
Sheehan, John, Dunahay, Terri, Benemann, John and Roessler, Paul. A Look Back at the U.S. Department of Energy's Aquatic Species Program -
Biodiesel from Algae, NREL/TP-580-24190, Golden, CO: NREL, July 1998.
Singh, Anoop, and Olsen, Stig Irving., "A Critical Review of Biochemical Conversion, Sustainability and Life Cycle Assessment of Algal Biofuels." Applied Energy 88
(2011), pp. 3548 - 3555.
Singh, Anoop, Poonam, Singh Nigam, and Murphy, Jerry D., "Mechanism and Challenges in Commercialization of Algal Biofuels." Bioresource Technology 102
(2011), pp. 26 - 34.
Strahan, David, "A Tank of the Green Stuff." New Scientist, Vol. 199, No. 2669, 16 August 2008, pp. 34 - 37.
Subhadra, Bobban G., "Sustainability of Algal Biofuel Production Using Integrated Renewable Energy Park (IREP) and Algal Biorefinery Approach."
Energy Policy 28, (2010), pp. 5892 - 5901.
Synthetic Genomics. Press Release: "ExxonMobil and Synthetic Genomics, Inc. Advance Algae Biofuels Program with New Greenhouse," dated July 14, 2010, viewed online
August 2011 at www.syntheticgenomics.com/media/press/071410.html
Templer, Laura, "Synthetic Biology: Injecting New Life into the Chemical Industry," Chemical Week, December 13, 2010, pp. 24 - 25
U.S. Defense Logistics Agency, Green Initiative for Fuels Transition Pacific, presentation chart statistic, available online at
www.usda.gov/documents/morning_speaker_PACOM.pdf.
U.S. Department of Energy, Office of Energy Efficiency and Renewable Energy, Biomass Program, "Integrated Biorefineries: Biolfuels, Biopower and Bioproducts," DOE/EE-0767, July 2012. Viewed online/downloaded July 2012 at
www1.energy.gov/biomass/pdfs/ibr_portfolio_overview.pdf.
U.S. Department of Energy, Office of Energy Efficiency and Renewable Energy, Biomass Program, "Solazyme Integrated Biorefinery: Diesel Fuels from Heterotrophic Algae," viewed online July 2012
at www1.eere.energy.gov/biomass/pdfs/ibr_arra_solazyme.pdf.
U.S. Department of Energy, Office of Energy Efficiency and Renewable Energy, Office of the Biomass Program, National Algal Biofuels Technology Roadmap, Washington, D.C.:
U.S. Department of Energy, May 2010.
U.S. House of Representatives, HR 6, Energy Independence and Security Act of 2007, 110th Congress, First Session, Public Law 110-140, 121 Stat. 1492 - 1801, Washington, D.C.:
US GPO, December 19, 2007.
Ugwu, C.U., Aoyagi, H., and Uchiyama, H., "Photobioreactors for Mass Cultivation of Algae," Bioresource Technology 99 (2008),
pp. 4021 - 4028.
Wehrum, William, testimony in Implementation of the Provisions of the Energy Policy Act of 2005, hearings before the Committee on Energy and Natural Resources, U.S.
Senate, 109th Congress, 2nd Session, on Electricity Reliability Provisions, Nuclear Power Provisions, Next Generation Nuclear Plant, and Renewable Fuel Standard and the Future Potential of Biofuels, May - June 2006, Washington D.C.: U.S. GPO,
2006.
To return to the top of the
page, click
here.
To return to the essay archives, click
here.

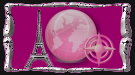

Follow www.dorothyswebsite.org on TWITTER!
"Like" www.dorothyswebsite.org on FACEBOOK!
Home | 
Essays | Poetry | Free Concerts | Links | 2014 Extras |
About the Site Featured Artists | 2014 Website Special Guests | News
|
|